Aluminum nitride (AlN) is a high-performance material with high thermal conductivity (320 W·m⁻¹·K⁻¹), excellent electrical insulation (>10¹⁴ Ω·cm), and strong mechanical properties. Its low dielectric constant (8.0 at 1 MHz) and minimal dielectric loss (tanδ = 10⁻⁴) make it ideal for electronics.
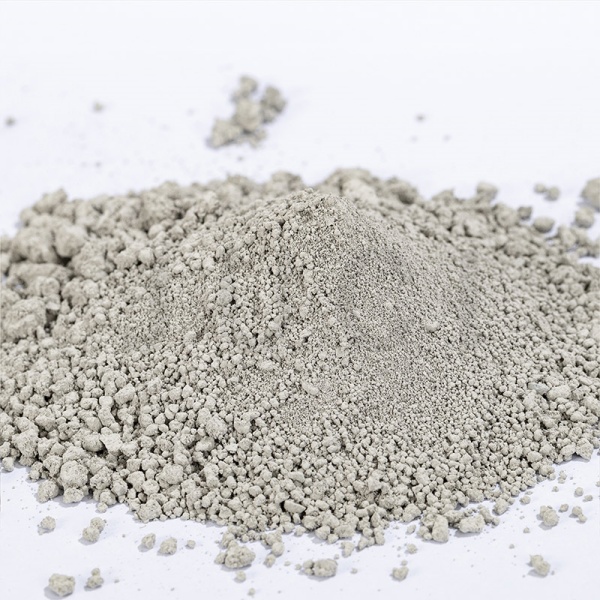
Key applications include:
Power device packaging
High thermal conductivity AlN ceramic substrates
Electrostatic chucks' material for semiconductor processing
Excellent insulation ceramic components ( ceramic heaters,ceramic nozzles)
AlN combines thermal management, electrical resistance, and durability for advanced industrial use.
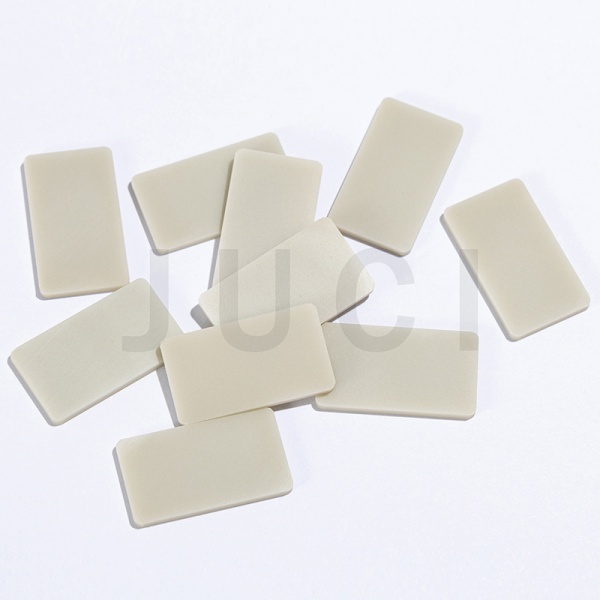
AlN ceramics are sintered from AlN powder, and high-quality AlN powder is a prerequisite for achieving high-performance AlN ceramics. The preparation of AlN powder significantly impacts the sintering, forming, and thermal conductivity of the final product. Industrially, there are three main methods for producing AlN powder: direct nitridation, self-propagating high-temperature synthesis (SHS), and carbothermal reduction.
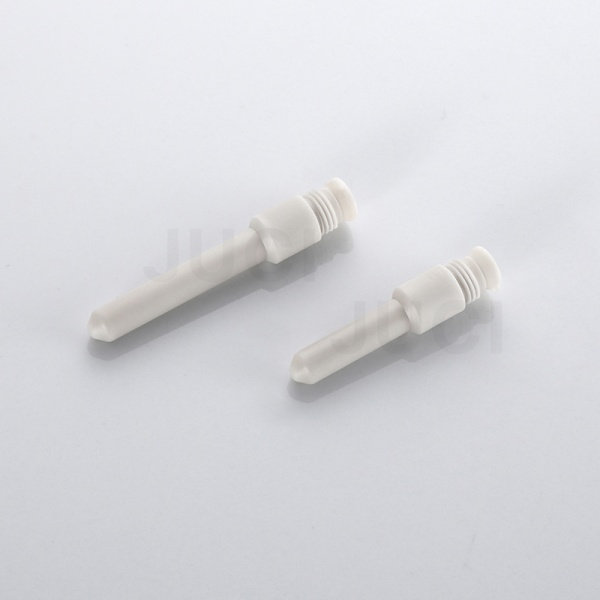
1. Principle of the Carbothermal Reduction Method
The carbothermal reduction method typically uses aluminum compounds (such as alumina or aluminum hydroxide) and excess elemental carbon or organic carbon as raw materials. These are reacted in a nitrogen (N₂) or ammonia (NH₃) atmosphere at high temperatures. The product is then decarburized in an oxidizing atmosphere at 500–700°C to obtain AlN powder. This method yields powder with low oxygen content, high purity, narrow particle size distribution, and regular particle morphology.
The reaction mechanism can be summarized as follows:

①Reduction of alumina: Carbon reduces alumina to form intermediate products such as Al(g) and Al₂O(g).
②Nitridation: Aluminum reacts with nitrogen to form AlN.
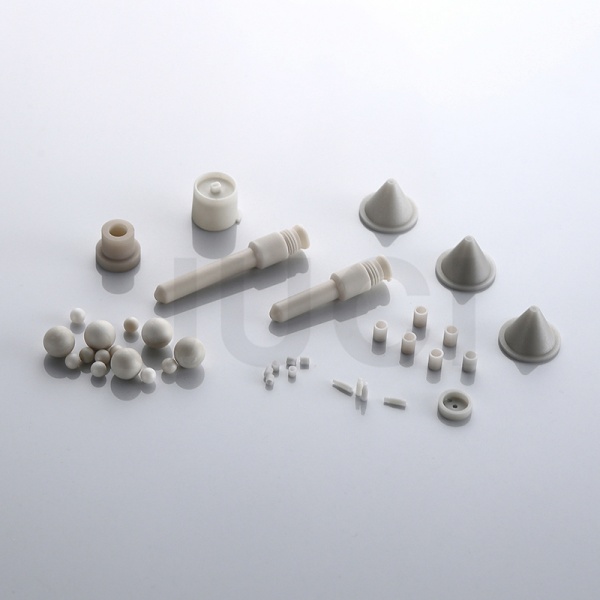
The reaction mechanism of carbothermal reduction can be categorized into gas-solid and solid-solid reactions. Experimental observations of aluminum vapor emission peaks support the formation of gaseous aluminum intermediates under specific conditions. The gas-solid reaction explains mass loss during the process and the mass transfer involved in whisker growth. Meanwhile, the solid-solid reaction mechanism accounts for the morphological continuity between the product and precursor, as well as the formation of intermediate compounds such as Al-O-C and Al-C-N during the conversion of Al₂O₃. This mechanism is more widely accepted.
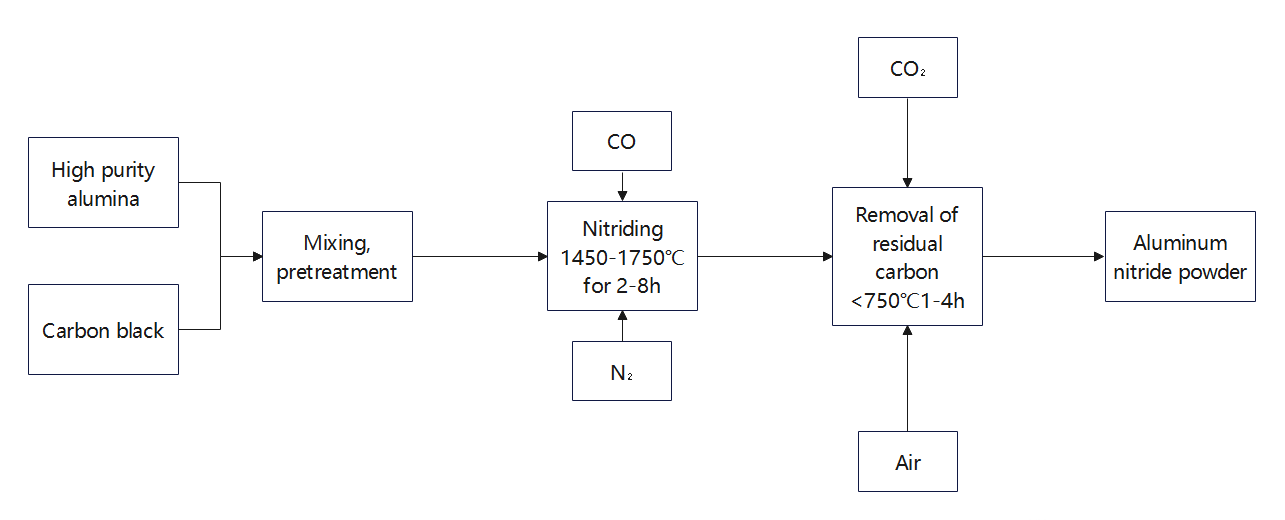
The AlN powder manufacturing process mainly includes ball milling and mixing, nitridation synthesis, low-temperature decarburization, and AlN crushing/recovery.
2. Process Characteristics of Carbothermal Reduction
The carbothermal reduction method offers advantages such as abundant raw materials, simple processing, and suitability for large-scale production. The synthesized powder exhibits high sphericity, purity, fine particle size, narrow size distribution, and good dispersibility, making it the primary industrial method for AlN powder production. Compared to direct nitridation and SHS, carbothermal reduction yields better sphericity and higher purity AlN powder .
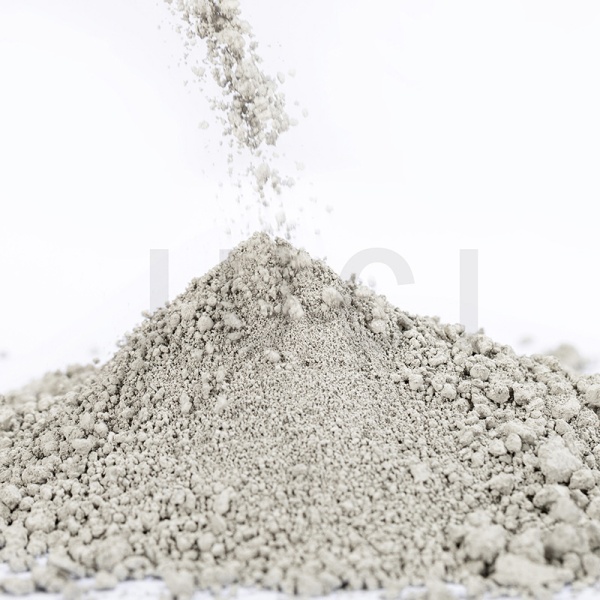
About Xiamen Juci Technology Co., Ltd.
Xiamen Juci Technology Co., Ltd. is a high-tech enterprise specializing in the research, development, production, and sales of high-performance ceramic materials. The company is committed to providing high-quality aluminum nitride series products and solutions for industries such as electronics, semiconductors, and aerospace, earning widespread trust from customers with its exceptional quality and service.
Media Contact:
Xiamen Juci Technology Co., Ltd.
Phone: +86 592 7080230
Email: miki_huang@chinajuci.com
Website: www.jucialnglobal.com