N-Phenylmaleimide (N-PMI) is a powerful monomer that plays a significant role in improving the heat resistance, durability, and overall performance of plastics and composites. It is widely used in industries where materials are subjected to high temperatures, mechanical stress, and harsh environmental conditions. In this blog, we will explore how N-phenylmaleimide enhances heat resistance and durability in plastics and composites, making them suitable for critical applications in automotive, electronics, and industrial sectors.
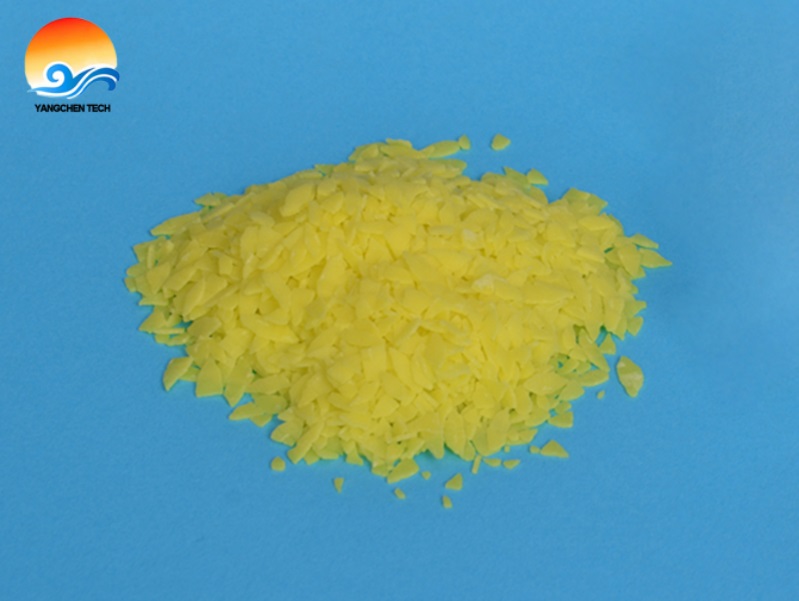
What is N-Phenylmaleimide (N-PMI)?
N-Phenylmaleimide manufactured by Yangchen Tech is a high-performance monomer with a maleimide functional group and a phenyl group that makes it highly reactive. This chemical structure allows it to copolymerize with other monomers such as styrene, acrylonitrile, and methyl methacrylate to produce heat-resistant polymers with enhanced thermal stability and mechanical properties.
Specification
Appearance |
Melting point |
Purity |
Solubility |
Yellow crystalline powder or flakes |
85-90℃ |
>99% |
Soluble in organic solvents |
Key Benefits of N-Phenylmaleimide in Plastics and Composites
Improved Heat Resistance
One of the most important benefits of N-phenylmaleimide is its ability to increase the heat resistance of plastics and resins. When incorporated into polymers such as ABS (Acrylonitrile Butadiene Styrene), PVC (Polyvinyl Chloride), and PMMA (Polymethyl Methacrylate), N-phenylmaleimide significantly raises the heat distortion temperature (HDT) of the material. This means the material can endure higher temperatures before it begins to deform, making it ideal for applications where the product is exposed to extreme heat.
Example: By adding only 1% N-phenylmaleimide as a copolymerization monomer in ABS, the heat distortion temperature can be improved by up to 2°C. When 15% N-phenylmaleimide is used, the heat resistance of ABS can reach 125–135°C, which is significantly higher than untreated ABS.
Enhanced Durability and Mechanical Strength
N-Phenylmaleimide improves the mechanical properties of plastics and composites by enhancing their tensile strength, hardness, and impact resistance. This results in materials that are not only heat-resistant but also more durable and able to withstand the mechanical stresses they face in demanding environments.
Durability in High-Temperature Environments: For applications in industries such as automotive and aerospace, where components experience both high heat and mechanical wear, N-phenylmaleimide-modified polymers provide superior long-term durability.
Increased Hardness: The incorporation of N-phenylmaleimide increases the hardness of the resin, making it resistant to scratches, wear, and other forms of mechanical damage.
Improved Chemical Stability
N-Phenylmaleimide also provides enhanced chemical resistance in modified resins. This makes it particularly useful in applications where materials are exposed to aggressive chemicals, solvents, and oils. The chemical stability provided by N-phenylmaleimide ensures that the polymer retains its properties even in harsh industrial conditions.
Applications of N-Phenylmaleimide in Plastics and Composites
Automotive Industry
In the automotive sector, N-phenylmaleimide-modified polymers are used for under-the-hood components, interior panels, and other automotive parts exposed to heat and mechanical stresses. The improved heat resistance and durability make these materials ideal for critical applications like engine covers, electrical connectors, and dashboards.
Electronics and Electrical Components
N-Phenylmaleimide is commonly used in printed circuit boards (PCBs), connectors, and electrical insulators. As electronics are often exposed to heat generated during operation, N-phenylmaleimide enhances the thermal stability of the materials, ensuring that electronic components continue to perform reliably over time.
Aerospace and Industrial Applications
N-Phenylmaleimide-modified composites are used in high-performance aerospace applications, where materials need to perform well in both high-temperature and high-stress conditions. This includes structural components, heat shields, and composite parts used in aircraft and spacecraft.
Consumer Electronics
Devices such as smartphones, tablets, and laptops, which generate heat during use, can benefit from plastics and composites modified with N-phenylmaleimide. It improves the thermal conductivity and long-term reliability of the materials, ensuring that electronic devices stay durable even under prolonged heat exposure.
How N-Phenylmaleimide Works in Polymer Modification
When N-phenylmaleimide is introduced into a polymer matrix, it undergoes copolymerization with other monomers such as styrene, acrylonitrile, or methyl methacrylate. This process results in a crosslinked polymer network that enhances the heat resistance and mechanical properties of the final product. The maleimide functional group forms strong bonds with the polymer backbone, improving the material's overall thermal stability, chemical resistance, and durability.
Why Choose Yangchen Tech for N-Phenylmaleimide?
At Yangchen Tech, we are committed to providing high-quality N-phenylmaleimide that meets the most demanding industry standards. Our N-phenylmaleimide is manufactured with 99.5% purity, ensuring consistent performance and reliability in various applications. We are also a trusted supplier for polymer modification solutions, offering cost-effective and customized solutions for industries that require high heat resistance and durability.
Our R&D expertise and industry knowledge allow us to provide tailored solutions that optimize the performance of your polymers and composites. Whether you need N-phenylmaleimide for automotive, electronics, or industrial applications, Yangchen Tech is your partner for high-performance materials.
N-Phenylmaleimide is a versatile and highly effective monomer for enhancing the heat resistance, mechanical strength, and chemical stability of plastics and composites. By incorporating N-phenylmaleimide into polymers, manufacturers can produce materials that perform reliably in extreme temperatures and harsh environments. Whether for automotive, aerospace, or electronics, N-phenylmaleimide is a key ingredient in producing high-performance materials that meet the toughest demands.
Contact Yangchen Tech today to learn more about how N-phenylmaleimide can improve your polymer formulations and help you achieve superior heat-resistant and durable materials for your applications.