
Background
Electronic packaging glue is used to package electronic devices. It is a type of electronic glue or adhesive that performs sealing, encapsulation or potting. After being packaged with electronic packaging glue, it can play the role of waterproof, moisture-proof, shockproof, dustproof, corrosion-resistant, heat dissipation, confidentiality, etc. Therefore, electronic packaging glue needs to have the characteristics of high and low temperature resistance, high dielectric strength, good insulation, and environmental safety.
Why choose epoxy resin?
With the continuous development of large-scale integrated circuits and the miniaturization of electronic components, the heat dissipation of electronic components has become a key issue affecting their service life. There is an urgent need for high thermal conductivity adhesives with good heat dissipation performance as packaging materials.
Epoxy resin has excellent heat resistance, electrical insulation, adhesion, dielectric properties, mechanical properties, small shrinkage, chemical resistance, and good processability and operability after adding curing agent. Therefore, currently, many semiconductor devices abroad are encapsulated with epoxy resin.
The development of epoxy resin
With the increasing calls for environmental protection and the increasing performance requirements of the integrated circuit industry for electronic packaging materials, higher requirements have been put forward for epoxy resins. In addition to high purity, low stress, thermal shock resistance and low water absorption are also issues that need to be solved urgently.
In response to problems such as high temperature resistance and low water absorption, domestic and foreign research has started from molecular structure design, focusing mainly on blending modification and the synthesis of new epoxy resins. On the one hand, biphenyl, naphthalene, sulfone and other groups and fluorine elements are introduced into the epoxy skeleton to improve the moisture and heat resistance of the material after curing. On the other hand, by adding several types of representative curing agents, the curing kinetics, glass transition temperature, thermal decomposition temperature and water absorption of the cured product are studied, in an effort to prepare high-performance epoxy resins for electronic packaging materials.
Introduction of several special epoxy resins for electronic packaging
1. Biphenyl type epoxy resin
The tetramethyl biphenyl diphenol epoxy resin (its structure is shown in the figure) synthesized by the two-step method exhibits high heat resistance, good mechanical properties and low water absorption after being cured by DDM and DDS. The introduction of the biphenyl structure greatly improves the heat resistance and moisture resistance, which is conducive to its application in the field of electronic packaging materials.

2. Silicone epoxy resin
Another research hotspot in the field of electronic packaging is the introduction of silicone segments, which can not only improve heat resistance, but also enhance toughness after epoxy curing. Silicon-containing polymers have good flame retardant properties. The low surface energy of silicon-containing groups causes them to migrate to the resin surface to form a heat-resistant protective layer, thereby avoiding further thermal degradation of the polymer.
Some researchers have used chlorine-terminated organosiloxane polymers to modify bisphenol A epoxy resins, generating Si-O bonds through the reaction of terminal chlorine with the hydroxyl groups on the epoxy chain. The structural formula is shown in the figure below.
This method increases the cross-linking density of the cured resin without consuming epoxy groups, which not only toughens the resin but also improves its heat resistance and impact resistance.
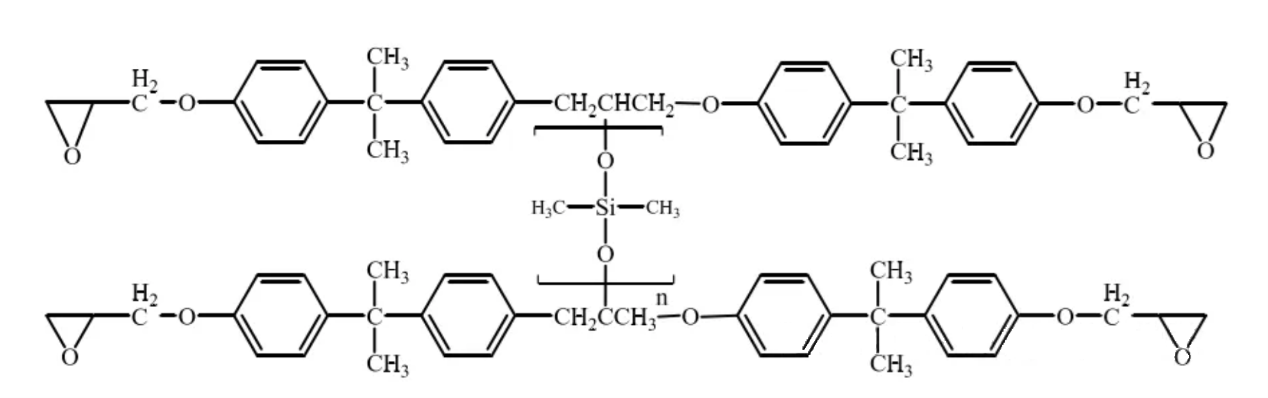
3. Fluorinated epoxy resin
Fluorine-containing polymers have many unique properties. Fluorine has the greatest electronegativity, the interaction between electrons and nuclei is strong, the bond energy between chemical bonds with other atoms is large, and the refractive index is low. Fluorine-containing polymers have excellent heat resistance, oxidation resistance and chemical resistance.
Fluorinated epoxy resin has the properties of dustproof and self-cleaning, heat resistance, wear resistance, corrosion resistance, etc. It can also improve the solubility of epoxy resin. At the same time, it has excellent flame retardancy, becoming a new material in the field of electronic packaging.
The fluorinated epoxy resin synthesized in the laboratory is liquid at room temperature and has extremely low surface tension. After curing with silanamine at room temperature or fluorine anhydride, an epoxy resin with excellent strength, durability, low surface activity, high Tg and high ultimate stability can be obtained. The synthesis steps are:
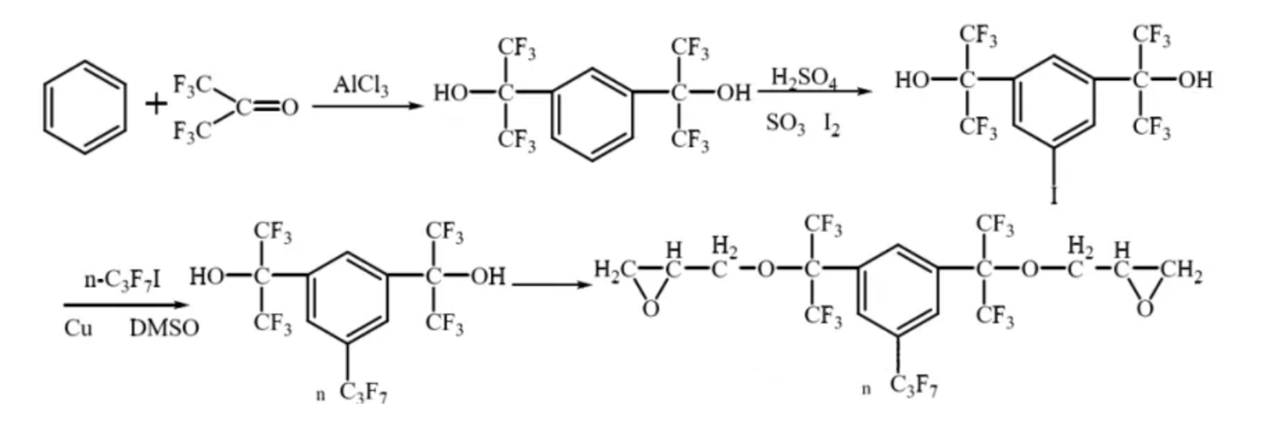
4. Containing dicyclopentadiene epoxy resin
Dicyclopentadiene o-cresol resin can be synthesized by reaction, the reaction formula is shown in the figure below. The resin is cured with methyl hexahydrophthalic anhydride and polyamide curing agent, and the Tg of the cured product is 141°C and 168°C respectively.
There is a new type of low-dielectric dicyclopentadiene epoxy resin (see figure below) whose performance is comparable to that of commercial bisphenol A epoxy resin, with a 5% heat loss of more than 382°C, a glass transition temperature of 140-188°C, and a water absorption rate (100°C, 24h) of only 0.9-1.1%.
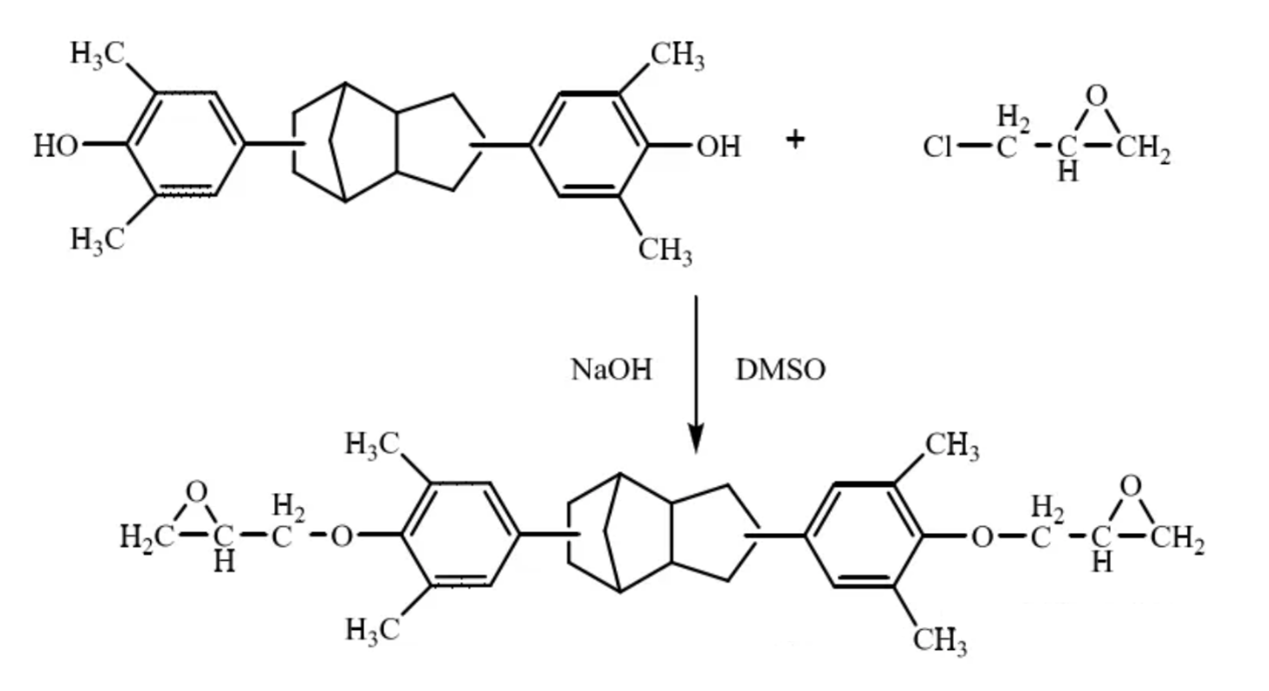
5. Naphthalene-containing epoxy resin
Some researchers have synthesized a new type of naphthalene-containing phenolic epoxy resin, the reaction formula of which is shown in the figure below. Its DDS cured product exhibits excellent heat resistance, with a Tg of 262°C and a 5% thermal weight loss of 376°C.
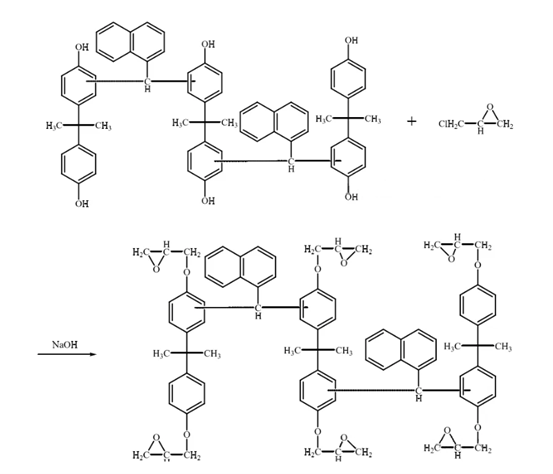
Synthesis of Bisphenol A-Naphthaldehyde Novolac Epoxy Resin
6. Alicyclic Epoxy resin
The characteristics of alicyclic epoxy resins are: high purity, low viscosity, good operability, high heat resistance, small shrinkage, stable electrical properties and good weather resistance. They are particularly suitable for high-performance electronic packaging materials with low viscosity, high heat resistance, low water absorption and excellent electrical properties. They are extremely promising electronic packaging materials.
The figure below shows the reaction process of a new type of heat-resistant liquid alicyclic epoxy compound. It can be obtained by etherifying alicyclic olefin diols with halogenated hydrocarbons to form alicyclic triolefin ethers, which are then epoxidized.
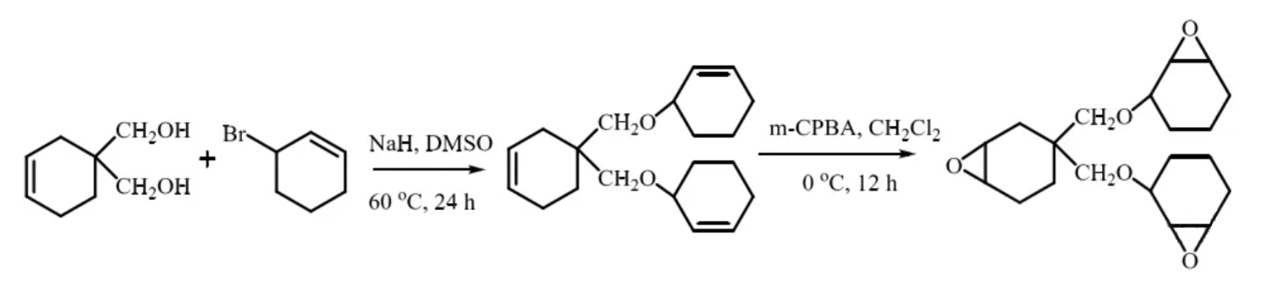
7. Blending modified epoxy resin
Blending is an important method to effectively improve material properties. In an epoxy matrix, adding another or several epoxy resins can improve one or several specific properties of the matrix material, thereby obtaining a new material with better comprehensive performance. In epoxy molding compounds, blending can achieve the goal of reducing costs and improving performance and processing performance.
In future production research, in order to enable epoxy resins to be fully used in the domestic electronic packaging industry, improving the preparation process technology, exploring the curing system of high-performance epoxy resins resistant to moisture and heat and medium-temperature moisture and heat-resistant epoxy resins, and preparing new epoxy resin modified additives are the development directions of this research field.
Nanjing Yolatech provides all kinds of high purity and low chlorine epoxy resins and special epoxy resin, including Bisphenol A epoxy resin, Bisphenol F epoxy resin, Phenolic epoxy resin, Brominated epoxy resin, DOPO modified phenolic epoxy resin, MDI modified epoxy resin, DCPD epoxy resin, Multifunctional epoxy resin, Crystalline epoxy resin, HBPA epoxy resin and so on. And we also could provide all kinds of curing agents or hardeners and diluents for epoxy resin application. Welcome new and old customers to inquire, we will provide you with the best service.